The benefits of process mapping your organisation can be vast and, if done properly, will deliver a substantial return on investment in time, money and effort. This article summarises the top ten benefits of process mapping, and explains why business process mapping can become one of your most valuable continuous improvement tools.
Why process map? Here are the top 10 reasons:
- For visibility of your end-to-end processes
- To show process and activity owners
- To support operational excellence
- To support induction and training
- To show compliance
- Identify and mitigate risk
- Enable business process analysis
- A ‘snapshot’ of your business
- To evidence change
- Enable continuous improvement
1. Visibility of your end-to-end processes
Process mapping the end-to-end processes of an organisation gives employees visibility of where what they do fits into the overall picture, and how it impacts not only other areas of the business but also ultimately the customer. Process mapping helps all employees understand where they fit within an organisation and how they work as a cross-functional team, which is a great first step towards breaking down siloed working.
2. Show process and activity owners
Everyone in an organisation performs a process, but who is ultimately responsible and accountable for specific activities? This can either be shown on the process map itself or stored within it.
3. Supports operational excellence
Process Mapping gives employees a chance to find the answers themselves rather than asking their colleagues or line manager. Process maps set out clearly what they should be doing, and can link to more detailed information on how they should do it in the form of:
- procedures
- guidance note/work instructions
- forms
- videos
- or anything that will help the employee to do their job
These are best shared through an intuitive business management system.
4. Support induction and training
Process maps are also a great resource for induction and training. Process maps communicate best practice in an intuitive and easy-to-understand way, supporting annual leave or sickness cover, new starters or if anyone leaves. Sharing maps via a Triaster Process Library, enables employees to search for processes based on their job role.
5. Show compliance
Process maps can be used to show compliance to regulatory standards such as ISO, FCA and SOX to name a few and also serve as a valuable resource for internal/external audits.
You can even get really specific and use information/data stored against each process map to show where the organisation is compliant to specific clauses or to evidence proper controls in place. This can then be exported as required.
6. Identify and mitigate risk
Process maps can be used to identify and show where Risk has been identified within the business and what controls are in place or need to be in place to mitigate the risk. Sharing visibility and educating employees about risk areas and controls is invaluable, as knowledgeable employees can then be proactive about mitigating risks.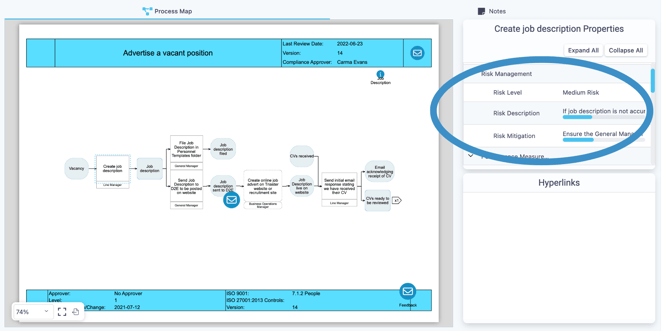
7. Enable business process analysis
As we have seen a process map can be a far more than a diagram of process steps, if you use the right process mapping tool, you can capture meta-data against each step of the process, which can then be used for process analysis.
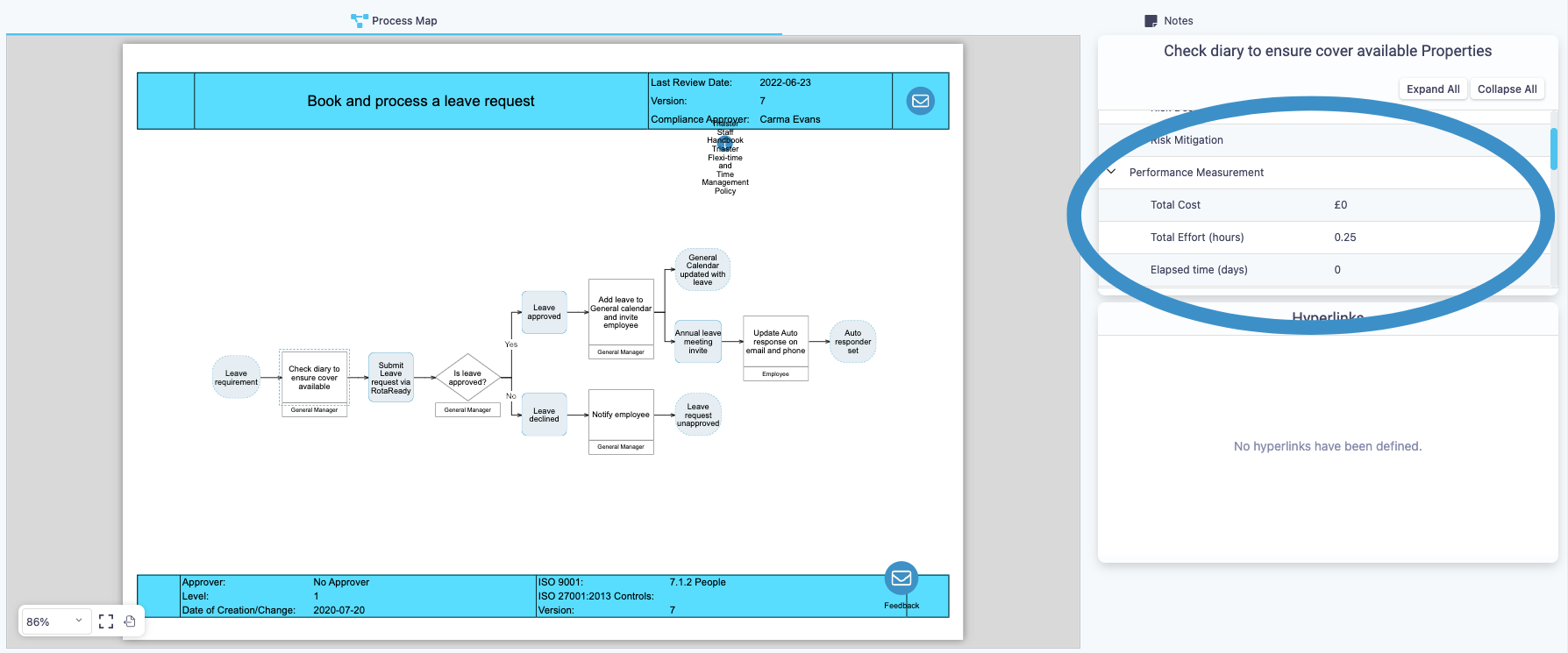
8. A ‘snapshot’ of your business
Mapped processes provide everyone in your organisation with a snapshot of how you do business today (your AS IS processes), and offers a mechanism to look at how you could do business tomorrow, more efficiently.
9. Evidence change
Once you have mapped your AS IS process this can be used as the baseline to look at improved ways of doing things (TO BE variants). If you have captured meta-data such as cost, total effort and waiting time against each activity you can effectively calculate if the changes proposed are actually going to add value to the business by reducing cost, reducing duplication and improving the overall service to the customer.
10. Enable continuous improvement
Once your To Be processes have been approved and implemented, they become your new AS IS processes, supporting your employees in all the ways mentioned above. It is from this new baseline that you can look again at ways to improve, making continuous improvement a reality.
In addition, organisations can show the trend of their continuous improvement by building an archive or history of process changes. This is useful for showing compliance to quality accreditations such as ISO 9001.
So how do I get started?
Triaster has been working in the process mapping and Business Process Management space for over 25 years and have developed Process Library so users can quickly and easily capture how everyone should be working, with easy to use, intuitive drag and drop process mapping. Get started by trying Process Library for free with our Process Library Free Plan.
Related Articles:
Process Mapping Techniques: 6 Methods to Create Process Maps
5 Process Mapping Tips: Getting People On Board, Not Making them Bored (video)
Related White Papers:
The Ultimate Guide to Business Process Mapping
The Complete Guide to Continuous Improvement in Business
This is an updated and refreshed edition of an article originally written in 2017.
Written by Giles Green
Giles joined Triaster in 2017 and is now our Business Improvement Director, working with organisations to increase efficiency, break down siloed working and improve their processes. Giles is passionate about solving business problems and how often a Process Library can do just that.