Your risk management process approach needs to be wrapped up in your quality strategy - in my experience, you can't really talk about one without also focusing on the other. This article deals with the cost of quality failure, 5 risk management process principles you need to put in place, putting a quality focus at the heart of your business and the type of tool you'll need to drive its success.
Managing Risk in Business: Learning From Quality Failure
Quality failures are nothing new of course. They also happen all the time on a limited basis. Small, everyday quality failures don’t make the news though.
Unfortunately, news worthy failures are nothing new either. Googling ‘quality failures’ immediately brings up:
- “5 Quality Failures that Shook the world”
- “The Top Five Quality Management System Failures of All Time”
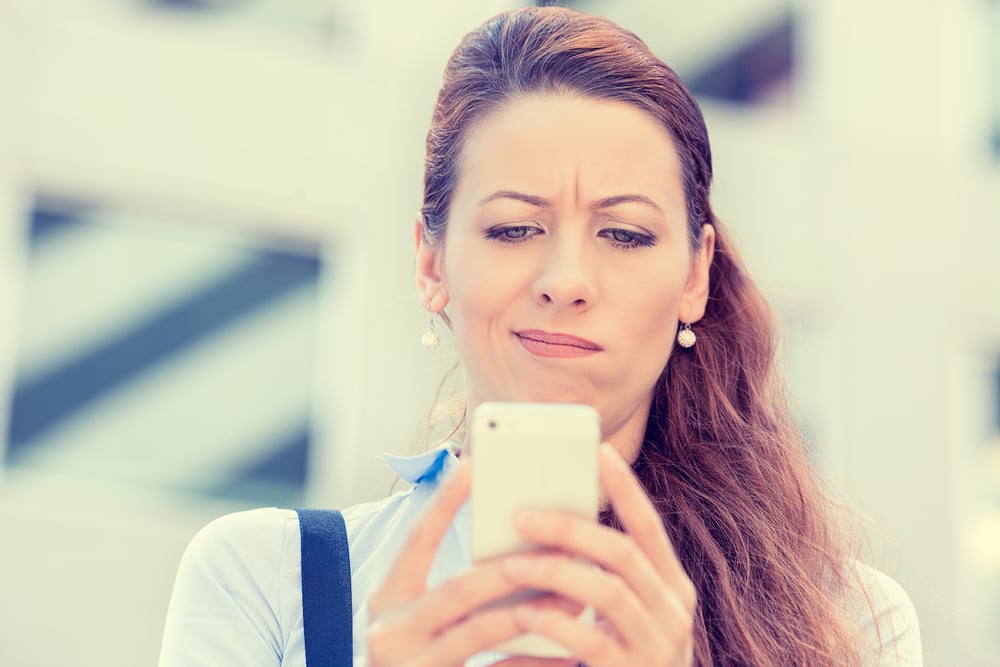
And examples of quality failures are listed that will never be forgotten:
- Hubble Telescope – images from an advanced technology, orbiting telescope were only slightly better than Earth based telescopes and very distant and faint objects (the very reason for having an orbiting telescope) could not be seen at all.
- iPhone 4 - touching the left side of the case at a certain spot interrupted the signal and dropped the call – not a great feature for a handheld device used primarily to make calls.
- The 2010 BP Deepwater Rig Explosion - this oil rig explosion was and still is the greatest manmade environmental disaster of US History.
The Cost of Quality Failure
Quality failures like these cost millions, not just in addressing the failure exposed, but in damage to the reputation of the brand.
A BBC news report in December 2015 entitled “Volkswagen: The scandal explained” stated that:
“With VW recalling millions of cars worldwide from early next year, it has set aside €6.7bn (£4.8bn) to cover costs". That resulted in the company posting its first quarterly loss for 15 years of €2.5bn in late October 2016.
But that's unlikely to be the end of the financial impact. The EPA has the power to fine a company up to $37,500 for each vehicle that breaches standards - a maximum fine of about $18bn.”
Ouch.
"We've totally screwed up," said VW America boss Michael Horn, while the group's chief executive at the time, Martin Winterkorn, said his company had "broken the trust of our customers and the public". Mr Winterkorn resigned as a direct result of the scandal. “
So...something to be avoided. No doubt about that.
Oddly though, there is often more doubt about how much should be invested in an organisation’s Quality Management System. Rarely is the investment in the Quality team and the Quality System in any way commensurate with the cost of a high profile quality failure.
This is because quality is often seen as all about ticking boxes, compliance, accreditation - an add-on to the core business of the organisation.
The Risk Management Process Principles:
There are five risk management process principles which you are probably not surprised to know are similar to Business Process Improvement principles and waste reduction principles.
1. Identify the Risk - This may seem like a rather obvious point, but you can't change what you can't see happening. In order to uncover the risk, you're going to need a tool that can identify all the processes in your organisation in order to find risky business areas.
2. Analyze the risk - Once you know what the risk is, it's potential impact on your business and the potential risk of quality failure.
3. Evaluate or Rank the Risk - Rome wasn't built in a day and you won't be able to address the risks found at once. That's why you need to evaluate risk, potential quality failure scenarios, then rank them so you can deal with the highest risks first
4. Treat the Risk - This step seems obvious...and it is. Once you have identified the biggest potential process failures it's time to act. Treat the risk that is the most apparent, by creating a quality strategy that mitigates risk and then work on your preventive plans and contingency plans in case things do go wrong.
5. Monitor and Review the Risk - Like a good doctor, after the risk is treated you'll need to monitor it and review it at regular intervals.
The Bonus Step that Never Ends: This isn't a 'do it once' project. It is a continual process that starts again with step one after step five has been completed.
Quality Strategy at the Heart of Every Organisation
The most effective way to mitigate against a quality failure is to put quality at the heart of your organisation.
And it is not just me saying this. The Chartered Quality Institute state on their website that:
“In short, we need to create a world with quality at the heart of every organisation.”
The longer statement can be found here.
So how is this done and how does it mitigate the risk of a quality failure?
Implement a Business Management System:
Your risk management process approach must be able to integrate into any business system you purchase. It must be given status and investment commensurate with the value that it can deliver.
This is done by integrating your Quality Management System with a Business Process Management system which extends (well beyond the quality department) organisation-wide.
Once this approach is adopted there is a platform in place to:
- Understand how the organisation currently works and where the risks currently are.
- Educate your employees in taking a process approach and a systemic dissatisfaction with the status quo, no matter how good the organisation is perceived to be.
- Identify clearly and visibly responsibility, accountability and process ownership, so that the person responsible for the quality improvement project/risk management project is known – not least by them.
- Model the risk of quality failure and the various approaches to mitigate against it.
- Implement improved processes with risks reduced.
- Adopt a Continuous Improvement culture.
This obviously doesn’t happen overnight and requires investment, leadership support and very often a change in culture. However, this has to be worth it to avoid being on the list that comes up when ‘quality failure’ is Googled.
Related articles:
Continuous Improvement: How do I create a culture of continuous improvement?
Written by Emma Harris
Emma was Operations Director for Triaster for nearly 20 years, during which time as well as learning and perfecting her BPM and process improvement skills, she honed her inbound marketing expertise. She now runs D2e - Designed to engage - which designs and develops bespoke, engaging, HubSpot CMS websites, that help your entire company to grow and scale. She is delighted to still be delivering Triaster's marketing, whilst also helping other companies turn their websites into their hardest working asset.