World Quality Day – ‘Sweet Dreams of Continual Improvement’ Conference
Isobel Witts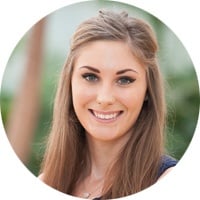
So you have been mapping your processes for some time. And you have made improvements by understanding what actually happens. But customers, products, markets and service propositions keep changing.
“We need to make a change, not too big because that would cost too much” says the manager “ … and it needs to be done quickly… …and we need to get it right.”
A regular scenario?
Which is why ‘continual improvement’ is necessary. But beware of the last phrase – ‘we need to get it right’.
The business analysis session gave me some good information that I will be able to use.
Keynote speaker Simon Feary, Chief Executive of the CQI (Chartered Quality Institute) highlighted the need to ensure we do things well. If we don’t then disaster happens quoting examples of processes where they weren’t managed well – VW (car emissions) and BP (Gulf of Mexico oil spill).
Apart from the obvious practical concerns in these and other examples it is the reputation of the company and even the industry with cars sales down by 1% that is mired, and it can take some time to recover that situation even longer to ‘fix’ itself. Quality is important but to have an effective means of ensuring that is not so easy in particular you have to convince the ‘Board’ to take cognisance of quality. They need the ‘business case’ as Simon says “You have to speak in the language that senior people understand. Protecting the organisation’s reputation or market position is certainly on their agenda, along with cost.”
How can we achieve that?
The workshop sessions started with Michael Cousins, MD of Triaster asking four working groups of delegates for their definition of an ‘end-to-end’ process, before embarking on the CQI Chocolate Challenge for World Quality Day 2015.
Enjoyed collaboration and exploration of ideas with other delegates. Working the problem, developing solutions.
The groups read the case study (about maintaining a consistent supply of cocoa beans to support chocolate bar manufacturing) and then organised the processes into groups to eventually create the ‘end-to-end’ process. Many discussions took place (fuelled by a supply of our own minibar chocolates!) to interrogate the key activities and identify the gaps. The outcome was to develop new processes to enhance and ensure the quality of the supply channel.
Later Mike unveiled the new facilities in the Triaster software which enables the collection and evaluation of processes, resources and costs of processes. Armed with this information ‘change managers’ can see how the new processes compare to the existing ones, producing the key parameters in a structured report format. How to convince those senior managers / the ‘Board’? Triaster’s well-structured report provides that ‘business case’ capability, it shows the costs of processes, and underlines the benefit of quality and the cost effectiveness for the new processes.
Most enjoyable interactive event, focused on continual improvement.
The challenge was set by the CQI, the event run by Triaster; we had a great day, to work, explore and network with delegates.
James Rowell is a Lecturer on Operations and Supply Chain Management at the University of Buckingham Business School.
Join us at our next Continual Improvement event:
Written by Isobel Witts
Isobel joined Triaster in September 2014 as our Customer Success Administrator. After about a year in the role she decided marketing was where her main interest lay and she began working with Emma as a new Triaster website was developed and the Triaster blog was started. The move was very successful, resulting in her moving full time into a marketing role, firstly at Triaster and subsequently for a local marketing agency.